Balancing separation efficiency versus energy consumption
40%
of energy consumption is
due to distillation columns
The process of distillation is very energy intensive and can contribute to more than 50% of plant operating costs. The challenge is to understand energy consumption on a real-time basis to balance against product quality.
hours to stabilize the distillation
unit after a flooding event
Flooding is a common abnormal process condition wherein the distillation column stops generating a separation, thus causing the quality of the top and/or bottom products to go off specification. This can negatively impact the performance, product throughput and energy efficiency of the distillation column.
Viewport with Column in Normal Operations
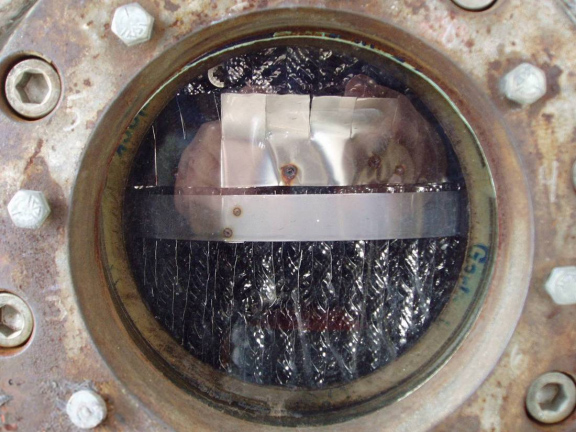
Viewport with Column Flooding
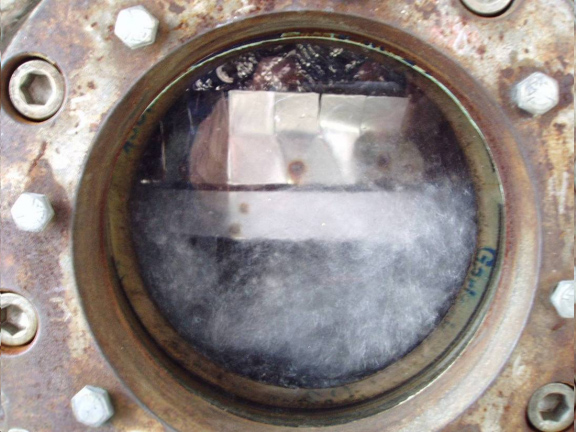
production loss due to
over-purifying and uses
over 12% excess steam
Feed streams can be overprocessed to meet quality standards increasing costs. In addition, a challenge is to avoid upset conditions that would affect product quality. If there is column flooding, weeping or foaming off-spec products will be produced resulting in expensive re-work.
excess energy consumed
due to unmanaged ambient
temperature swings
Ambient temperature fluctuations caused by weather events can cause distillation column upsets as temperature and pressure profiles change, affecting the liquid-vapor equilibrium. This can lead to less-than-optimal separation resulting in poor product quality.